Introduction:--
In textile industry, woven fabrics are produced by interlacing warp and weft yarn. Faulty woven fabrics hampers the total quality of woven garments such as shirt, pant, trouser, jacket etc. As a textile engineer you should know about the major woven fabric faults which produced during woven fabric manufacturing. As its importance this article has shown those woven fabric faults with their images.
Major Defects Found in Woven Fabric:
Various types of faults found in woven fabric has mentioned in the below:
- Bad selvedge,
- Broken ends or warp,
- Broken picks or weft,
- Loose warp,
- Loose weft or snarl,
- Double end,
- Tight end,
- Float of warp,
- Wrong end color,
- Miss pick,
- Double pick,
- Weft bar,
- Ball,
- Hole,
- Oil spot,
- Tails out,
- Temple mark,
- Reed mark,
- Slub,
- Thick and thin place.
All the above woven fabric faults have explained in the following:
1. Bad or defective selvedge:
Bad selvedge in woven fabric due to the faulty weaving. Here, warp ends being set too far apart for the thickness of the yarn or in finished fabric.

Defective selvedge
2. Broken ends or warp:
A defect in the woven fabric caused by a warp yarn that was broken during weaving or finishing.
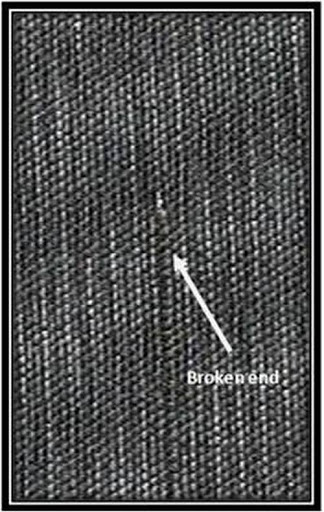
Broken ends
3. Broken picks or weft:
A filling yarn that is broken in the weaving of fabric.
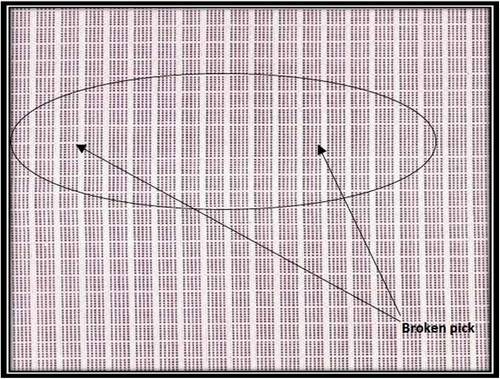
Broken picks
4. Loose warp:
This type of fault is produced in woven fabric when the tension of warp yarn is slow.

Loose-warp
5. Loose weft or snarl:
It is produced in woven fabric due to the looseness of filling yarn.

Loose weft
6. Double ends:
This kind of fault is produced in woven fabric when the two ends of warp sticks get together after sizing.

Double ends
7. Tight ends:
If the tension of warp yarn is more than the other ends present in the loom then this type of fault is produced in woven fabric.

Tight ends
8. Float of warp:
If someone pulls the fabric together the cloth roller intentionally or unintentionally then this kind of defect is produced in woven fabric.
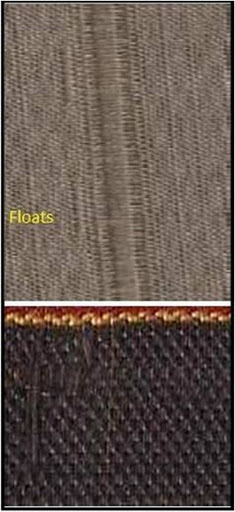
Float of warp
9. Wrong end color:
It is produced in woven fabric due to the wrong drawing of colored yarn.
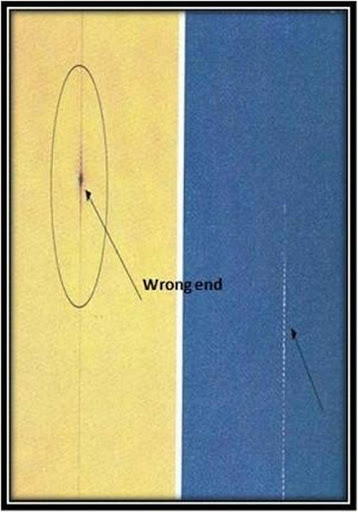
Wrong end color
10. Miss pick:
This kind of defect is produced in woven fabric when operator starts a stopped machine without picking the broken weft from the shade.

Miss pick
11. Double pick:
It is produced in woven fabric when the cutter don’t work properly.
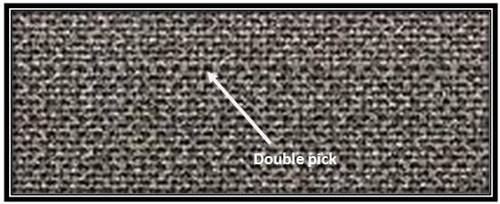
Double picks
12. Weft bar:
When count of yarn varies from one cone to another cone then a bar of weft will be appeared in fabric after weaving.
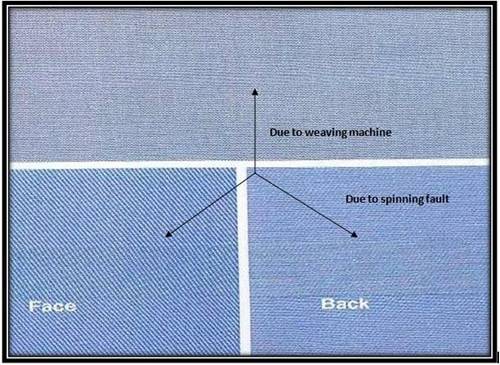
Weft bar
13. Ball:
If the warp is too much hairy then the reed will create ball in warp yarn in between reed and heald shaft. If the ball is small enough to pass through the dent of reed then those will form the ball in fabric.
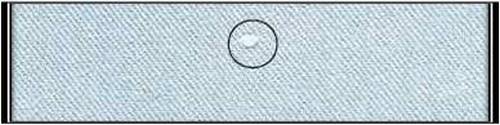
Ball
14. Hole:
A fabric imperfection in which one or several yarns are sufficiently damaged to create an opening.

Hole
15. Oil spot or stain:
Discoloration on a local area of a substrate that may be resistant to remove by laundering or dry cleaning. It occurs during spinning, weaving or finishing. It is also often seen in the woven fabric. It is also produced in woven fabric if too much oiling has done on the loom parts.

Oil-stain
16. Tails out:
This kind of fault is produced in woven fabric if the cutter doesn’t work properly.
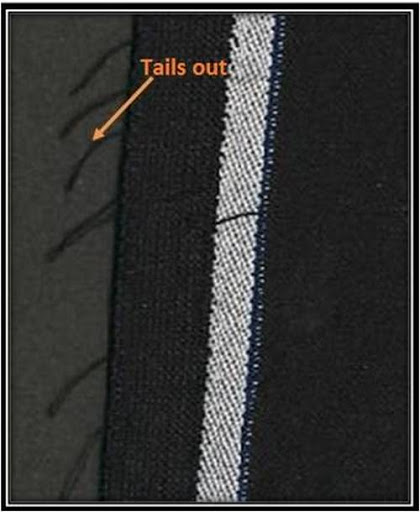
Tails out
17. Temple mark:
If the placement of ring in the temple bar is wrong or the pressure of temple to the fabrics is too high then this type of fault is produced.

Temple mark
18. Reed mark:
In woven fabric, a crack between the groups of warp ends either continuous or at intervals. It’s may be caused by the wrong drawing-in of the warp or damage to the reed wires.
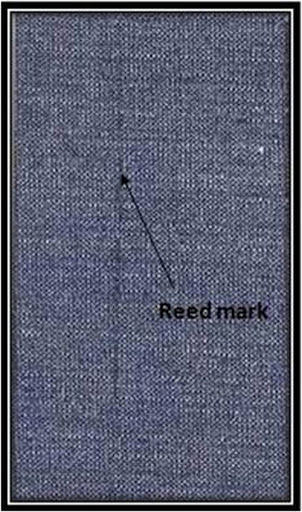
Reed mark
19. Slub:
If the yarn contains unexpected slub in it then those slub will be appeared in the fabric as a fault.

Slub
20. Thick and thin place:
Fabric defect in which fabric count varies more than a specified percentage from the intended count. If the thick or thin place is more than one inch (2.54cm) wide then it is considered as a major defect in fabric grading.
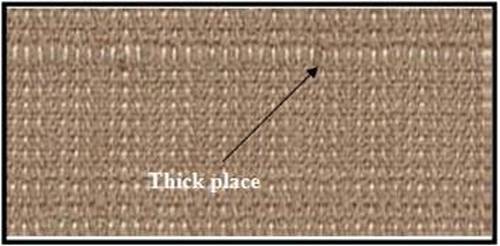
Thick place
A segment of yarn at least ¼ inch (0.6cm) long that is noticeably thicker than adjacent portions of yarn is called thick place. A segment of yarn at least 25% smaller in diameter than adjacent portions of yarn is called thin place.